Analog I/O Modules

Series
6000 analog I/O modules condition, amplify, filter and digitize signals
from virtually any transducer. All modules have conditioning &
amplifier per channel and nearly all modules allow for setting bridge
completion, shunt calibration, transducer power, gain, etc. individually
per channel. Following the conditioning/amplifier stage, multi-pole
Bessel or Butterworth analog filters are provided on each channel and
can be set or bypassed individually by program control. A number of the
modules include a high level analog output providing a
conditioned/filtered output to a redundant, external A/D system. A
16-Bit Successive Approximation A/D follows the analog filter stage.
Some modules use a single A/D with sample and hold while others have an
A/D per channel. Sample rates are programmable per channel to easily
accommodate mixing high and low speed measurements into a single data
stream. Programmable hardware based warnings and alarms are included in
the channel-by-channel architecture and are detected by digital output
modules in the system, providing an ultra-low latency control capability
directly from the data acquisition system.
|
Digital I/O Modules
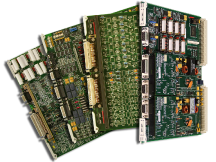
Series
6000 digital I/O modules record signals from frequency counters, flow
meters, encoders, discrete transducers, IRIG time, etc. which are often
part of the test environment. These digital signals are time aligned and
recorded alongside the system’s analog measurements. High
density digital inputs provide an opportunity to easily include facility
controls like switches, valve positions, relays, lights, etc. along
with the test data. Series 6000 digital I/O modules also provide outputs
generated by user command or automatically by Sequence, Alarms or DSP.
User generated outputs are accomplished in software while sequencers can
be programmed prior to a test and initiated by program or hardware
control. Alarm conditions preprogrammed on the analog side can
automatically generate digital outputs which are typically connected to
facility control systems or PLCs. A DSP adds powerful real-time
processing and is appropriate for PID control loops, derived parameter
calculations and a variety of other real-time operations.
|